LENS Engineering, Science, and Technology
A Robot with Muscle
Melding Living Tissue and a Plastic Body
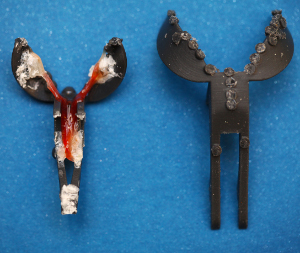
At right is the biohybrid robot's underside with the sea slug tissue; at left is a larger version shown right-side up.
Case Western Reserve researchers have combined a muscle from the sea slug with a 3-D-printed polymer to build a biohybrid robot—part living tissue, part machine. A future version might someday be deployed on an ocean floor to detect toxins, chemical leaks from underwater pipelines or even black boxes from downed planes.
While this isn’t the first time scientists have created a biobot, this model is better able to withstand varying temperatures, changing habitats and wet conditions.
Why even create biobots in the first place? Because they can interact safely with humans and the environment, said Victoria Webster-Wood, PhD (CWR ’12; GRS ’13, GRS ’17, mechanical engineering), who led the project as a graduate student in the university’s biorobotics lab, working closely with professors from the mechanical and aerospace engineering and biology departments. She remains at the university working as a research associate.
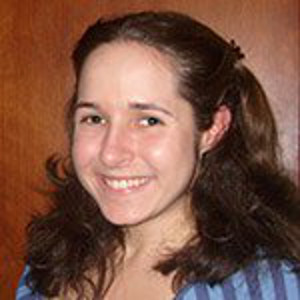
Victoria Webster-Wood, research associate
“If the device breaks down or gets lost, you’re not polluting the environment, you’re not going to damage native wildlife,” said Webster-Wood, who began working in the lab as an undergraduate. The research team now is working to make the device more organic by replacing the polymer with collagen from the skin of the sea slug, Aplysia californica. The researchers used heavy-duty glue to attach a Y-shaped mouth muscle to a sea-turtle-shaped polymer with two front legs and an elongated body. The resulting robot is about an inch long and moves 0.2 inches per minute, but future versions could be made larger, Webster-Wood said, by using bigger sea slugs or a bigger muscle from one.
The device’s energy source is sugar dissolved in the surrounding water. Among the next steps: determining how to enable the biobot to take that energy source with it, perhaps by enclosing the sugar water under a skin flap.