lens
Salt Solution
Rohan Akolkar is developing a greener way to make steel and process rare-earth metals
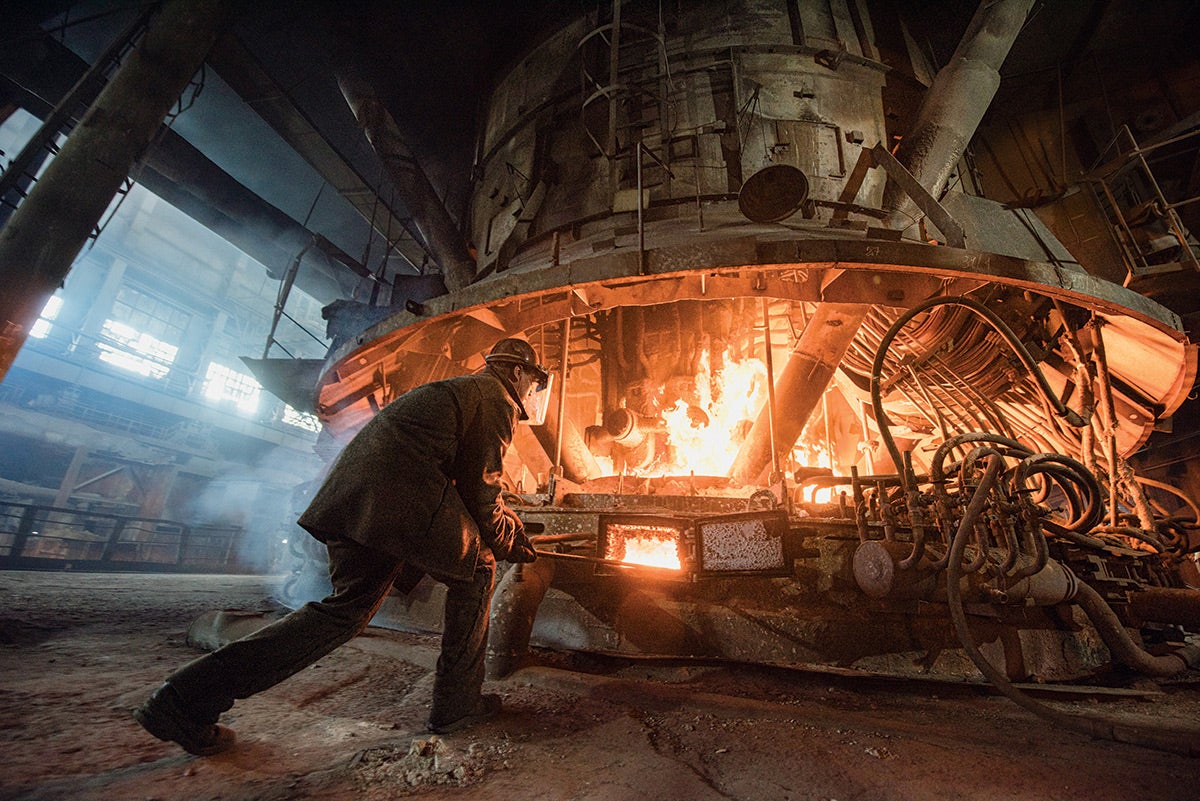
Every year, steel production pumps almost 3 billion tons of carbon dioxide (CO2) into our atmosphere—almost three times the amount produced annually by commercial air travel. And as demand keeps growing, Rohan Akolkar believes it's time for a new, greener way to make steel.
"We have no choice but to really come up with a revolutionary process that offers both sustainability and cost effectiveness," said Akolkar, PhD, professor of chemical engineering at Case Western Reserve.
The bulk of steel's greenhouse-gas emissions comes from the energy-intensive process of producing iron. In its natural form, iron ore is composed of molecules containing iron and oxygen. To separate the pure iron metal, steelmakers combine the ore with carbon at temperatures up to 1,700° Celsius. The process is a double whammy for the environment: It not only releases carbon dioxide as a byproduct, but many of the furnaces are powered by burning coal.
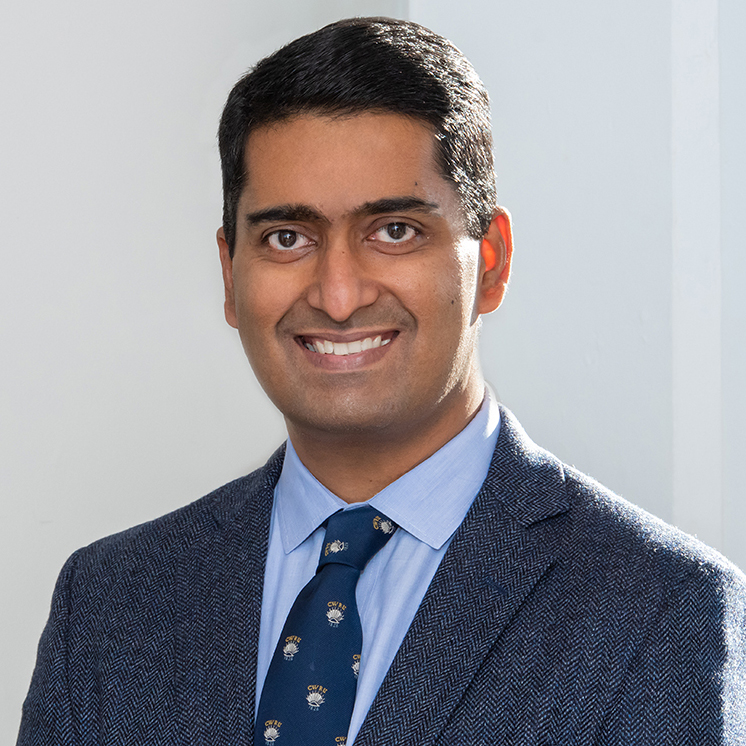
Rohan Akolkar
Akolkar, who serves as the Milton and Tamar Maltz Professor of Energy Innovation and the chief scientist at Pacific Northwest National Laboratory, is working on a greener solution. The key ingredient: salt.
When some salts get hot enough—about 500 degrees Celsius—they liquefy into a concentrated soup of charged particles. Mix ore particles into this molten salt and apply electric current, and the iron separates from the oxygen resulting in pure metal. The process, called molten salt electrolysis, is efficient and carbon-free, Akolkar said.
With several grants from the U.S. Department of Energy (DOE) and in collaboration with partners including Lawrence Livermore National Laboratory, Argonne National Laboratory and Cleveland Cliffs Inc., a major steelmaker, Akolkar is working to show the process can work efficiently enough to be economically competitive with conventional blast furnaces.
Molten-salt electrolysis is also a more sustainable way to purify rare-earth metals, materials that are ubiquitous in modern digital gadgets and essential for making the strong, powerful magnets inside green tech such as wind turbines and electric vehicle motors. Contrary to their name, rare-earths are not particularly rare, but are typically scattered in low concentration among other, less valuable materials. The conventional method for separating different types of rare-earths relies on environmentally damaging solvents and emits powerful greenhouse gases.
Some national security experts worry the United States depends too heavily on China for rare-earths, which are a key ingredient in U.S. military might. If the supply were cut off, everyday consumers and the armed forces would both feel the pinch.
To Akolkar, molten-salt electrolysis presents a unique opportunity to build a greener domestic rare-earths industry from the ground up. He and his colleagues have already demonstrated the process in the lab, with support from the DOE and its Critical Materials Innovation Hub. The next step is taking the process to factory scale.
"We are at an inflection point," Akolkar said. "Metals production is one of the biggest contributors to climate change. We can either do something about it now or, I fear if we don't, in 30 years, we may feel that we had the opportunity, but we missed it."
— KATE BECKER