lens
Striking a Chord
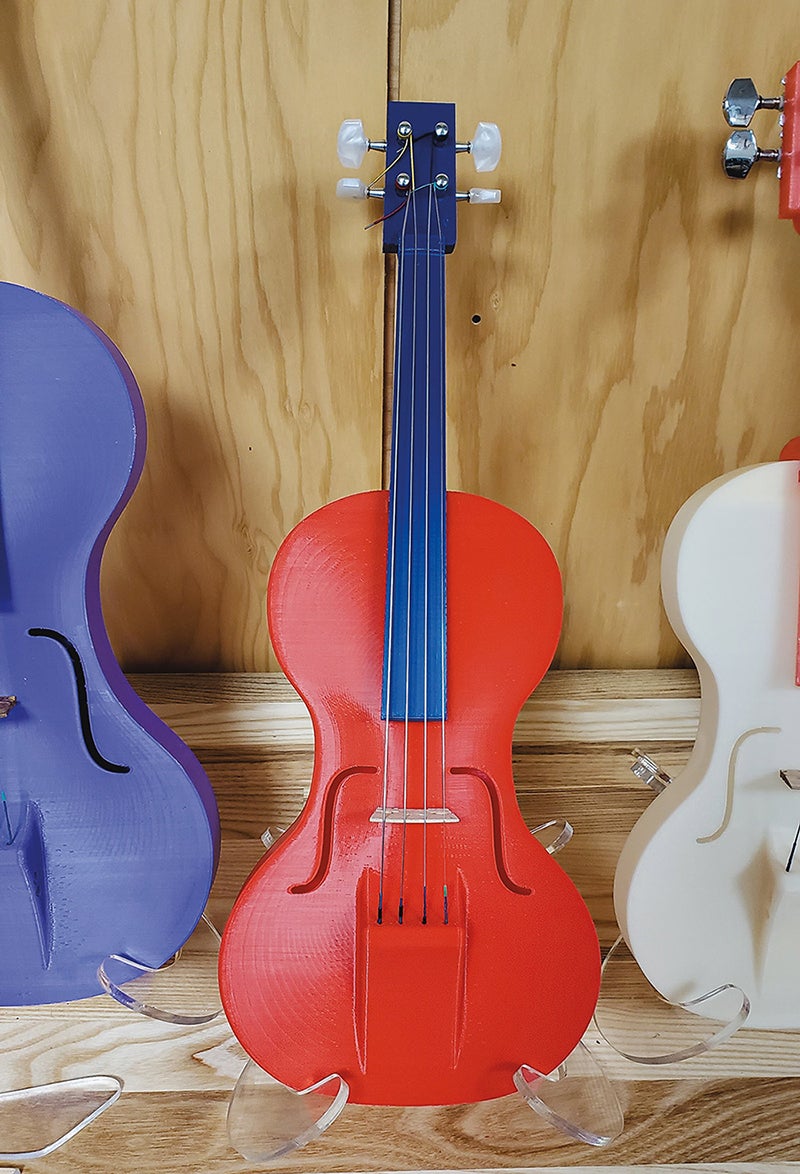
At this year’s CES—an international consumer-technology trade show—a fellow exhibitor walked up to 3D Music’s booth, skeptically eyeing the company’s violins.
He didn’t expect much from the 3D-printed plastic instruments that company founder Matthew Canel (CWR ’20; GRS ’21, mechanical engineering) developed at the Case Western Reserve University Larry Sears and Sally Zlotnick Sears think[box] innovation center as the focus of his master’s degree.
But the skeptic picked up a violin and played a scale, then selections including the Star Wars theme and Vivaldi’s “Spring.”
“He was too entranced to leave,” Canel recalled.
A childhood cello player, Canel was an undergraduate when he first encountered a 3D-printed violin. Printed by student technicians at Sears think[box] from online instructions, it emitted a lackluster sound. Canel knew he could do better.
He met with a violin maker and began designing a child-size violin that he said has solid acoustic quality, is durable, not susceptible to temperature fluctuations, stays in tune for extended periods and costs about $200. That’s half of what a comparable wooden violin might cost. Recently, the company also began producing full-size violins.
The target audiences include schools, music programs and individuals, said Ben Kaufman (CWR ’12; GRS ’13, engineering and management), head of business development for 3D Music, based at Sears think[box].
“We want to bring music to more people,” Canel said, “and prove that the violins can sound as good as your traditional instrument.”